As Spring arrives, the chilly memories of Winter fade, and concerns with thermal work clothing, ice removal operations and the structural integrity of materials in below-freezing conditions fade right along with them. The days become warmer. The sun shines brighter. It’s time to be outdoors.
While all this is true, LBS knows that Spring is actually the PERFECT time to plan for Winter. By getting a head start in the Spring, you save time, money and headaches on upcoming Winter projects.
Large projects, for example, that stretch over multiple seasons, may require special sequencing so that weather-dependent work is completed ahead of Winter conditions. By using the panelized LBS system, we are not as weather-dependent and save considerably on schedule and cost. For optimal results, switch the entire structural framing system over to the load-bearing steel stud LBS system.
Listed below are five essential reasons why the Light-weight Building Systems Inc. approach is ideal for building through adverse weather conditions.
1. LBS Steel is Strong, Ductile and Structurally Ready for Installation in All Year Round
LBS steel stud framing and panel erection on a job site is not restricted by weather conditions. Our steel does not warp, twist or bend when exposed to the elements, and it is not affected by cold temperatures. Also, steel does not absorb moisture. This is not the case with other building materials.
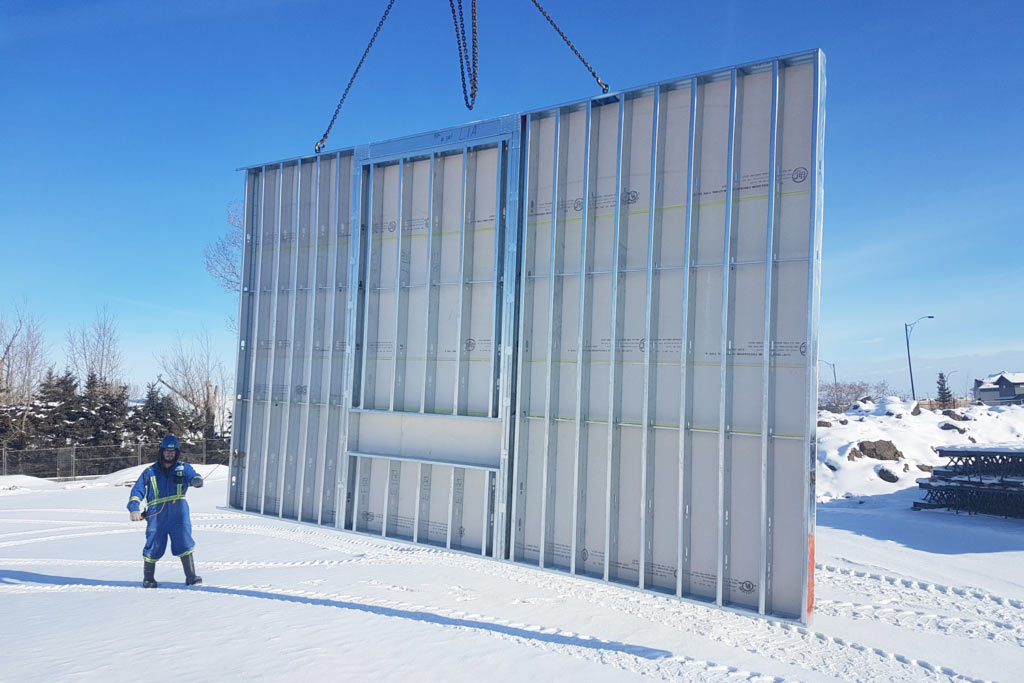
2. The LBS System Requires Less Heat and Hoarding in Cold Weather Conditions
Cast-in-place (CIP) concrete and structural steel projects tend to incur higher costs during wintertime versus other seasons.
The LBS system, on the other hand, typically requires less heating and no hoarding as our exterior steel stud walls are pre-panelized with exterior sheathing. The building shown on the left below is an LBS building, while the one on the right is a conventional concrete structure. Both buildings are at 14 weeks duration in schedule.
The photo below depicts how involved heating and hoarding can be with conventional concrete.
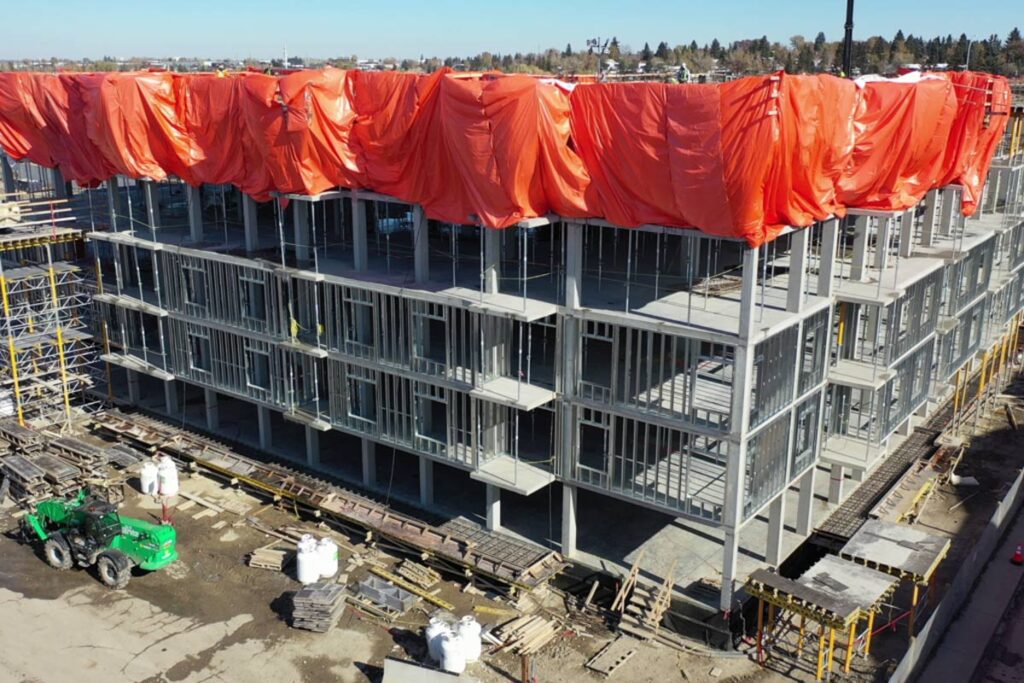
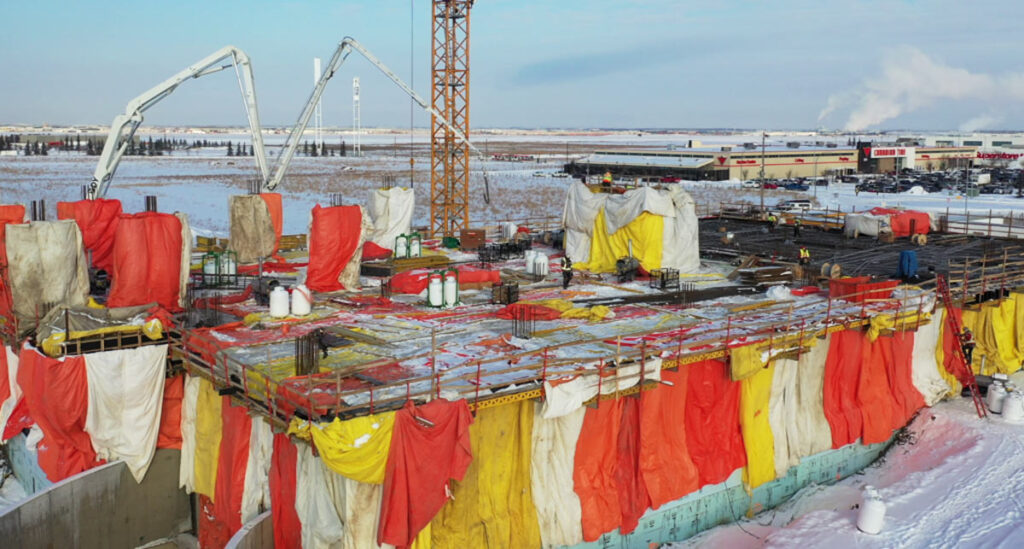
3. The LBS System Facilitates the Interior Trades’ Work During Winter Months
The exterior walls are completed with exterior sheathing so the interior work space can be managed, in order to maintain a comfortable work environment. Shoring is typically not required so trades can start immediately behind the structure. Once the LBS structure is completed on each floor level, the drywall, mechanical, electrical and plumbing (MEP) trades can begin their work. These trades don’t have to use their own equipment to create punchouts or alter the framing assemblies to accommodate their runs. LBS wall studs and floor joist systems provide factory-made punchouts and aligned structural members for ease of M&E installations.
Pre-designed and properly placed wall stud and floor joist members make interior installations faster. The predictability, accuracy and inherent features of steel studs and joists enhance overall job site productivity.
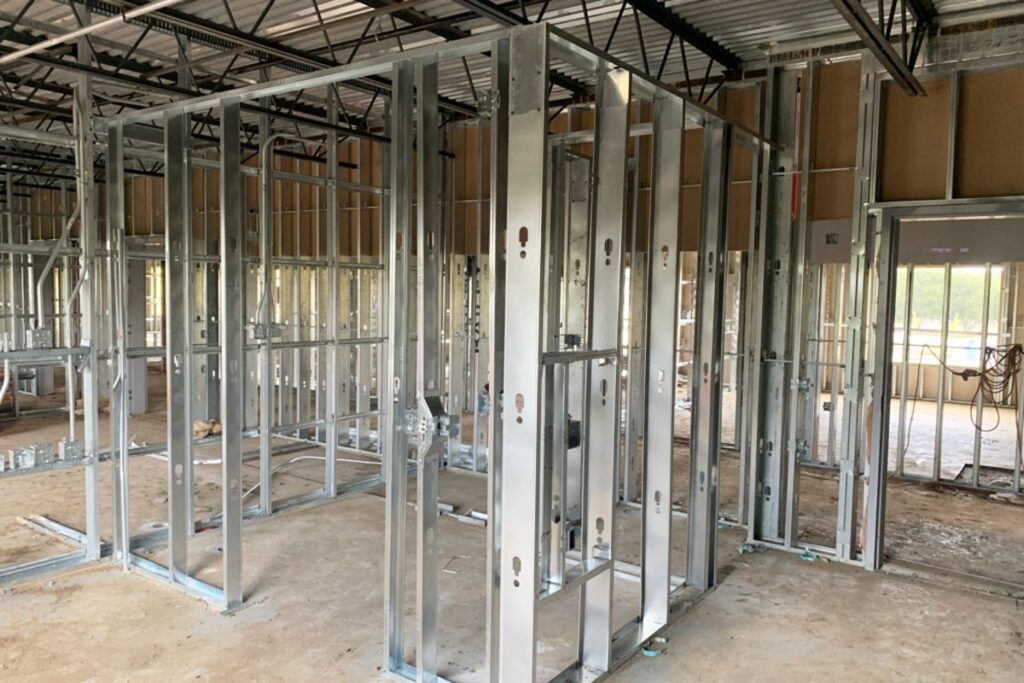
How can the Developer and General Contractor build a non-combustible building without a Canadian Winter interfering with the delivery timeframe? The solution is to use load-bearing LBS walls instead of cast-in-place concrete or concrete block and to have the concrete foundations poured by the end of summer.
By pouring the structure’s foundations in the Summer and installing load-bearing LBS framing during the Fall, a project can be completed early, which also saves considerably in carrying costs.
The above would be the best-case scenario, however, if a superstructure installation falls into Winter conditions, be proactive by using the LBS system to help avoid schedule delays and costly heating and hoarding.
5. LBS Panelization During Winter Months Saves Money
LBS steel is prefabricated. This work is done off site in our two fixed panel plants or on-site in our unique mobile panel plants, under controlled, regulated and safe conditions.
This Winnipeg project pictured below benefitted greatly by using a prefabricated structural system that could support a variety of exterior claddings. LBS exterior wall panels were finished with an Exterior Insulation Finishing System (EIFS). In using the combination of prefabricated LBS panels and EIFS cladding, the heated scaffolding for on-site stucco application was not required resulting in monetary savings for the owners.
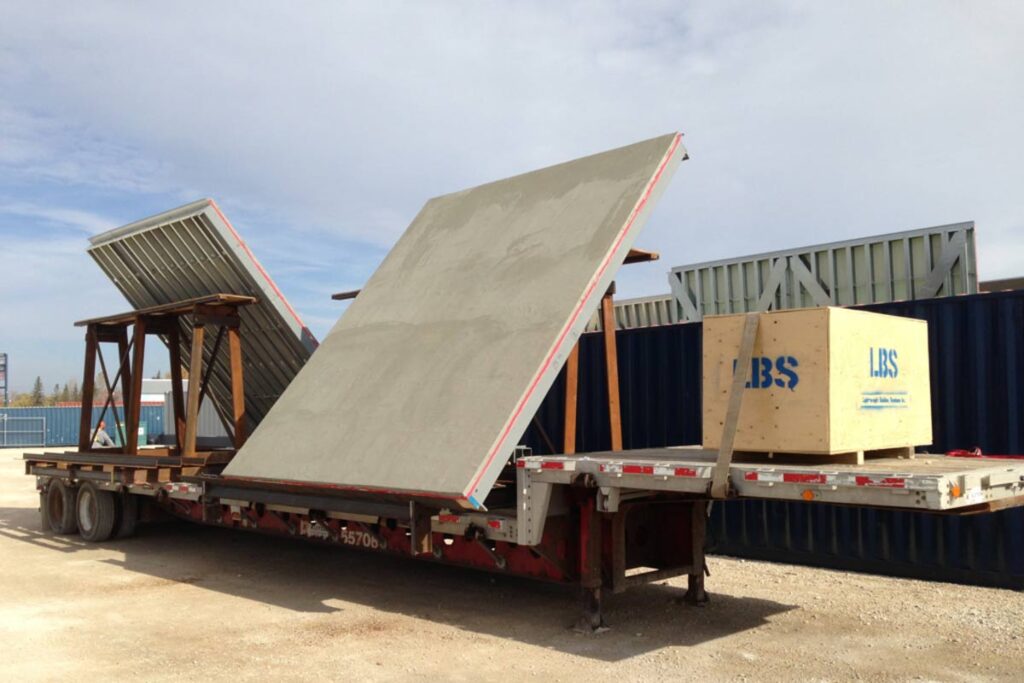
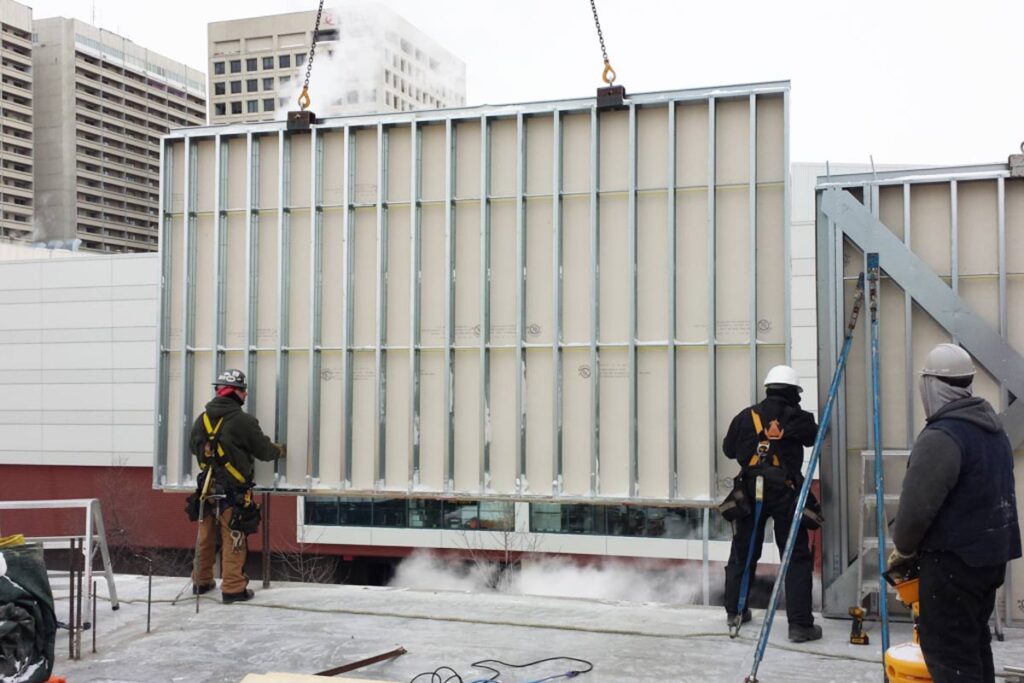